- 4000TON 油圧プレス(昭和50年)/前職にて
- ベニヤレース
- 茶運び(からくり)人形
- 30TON エアー・ハイドロプレス(動力:エアー)50TON油圧プレス
- テーブル旋回 30TON エアー・ハイドロプレス(動力:エアー)
- トムソン刃性能試験機
- 侍シリーズ/切屑の出ない切断機
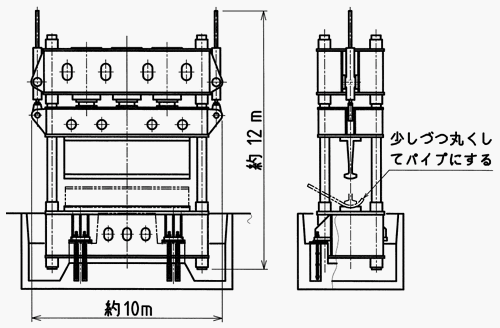
原子力用の厚肉パイプ(100mm以上)を製作するための油圧プレスです。
私が、ある会社に就職して7年目に担当した仕事で、設計はすべて私にまかされました。
350気圧(35MPa)の高圧を使用。 プレスの金額は当時のお金で 2億円でした。
設計に要した期間は1年半、その内強度計算を含む計算や検討に約 1年、図面作成に半年。
計算資料だけで、キングファイル3冊という大変なボリュームです。
当時350気圧(35MPa)というのは非常に高圧で、間違いなく稼動すると確信がもてるまで、専門の油圧メーカと相当な回数打ち合わせをしました。
製作過程でもいろいろ問題がありました。
75TONもある、上/下のフレームは 、名古屋で焼鈍出来る業者はありません。
大型の炉を持っている、大阪の業者に焼鈍を依頼しました。
しかし大きすぎて、昼間運ぶ許可が下りません。大型トレーラに載せ、夜1号線で大阪まで運びました。
さまざまな苦労の後、めでたく完成して納品し、お客様には非常に喜んでいただきました。
たいへんな経験でしたが、これが私の自信になり、その後の私の設計人生の大きなはげみになったことは言うまでもありません。
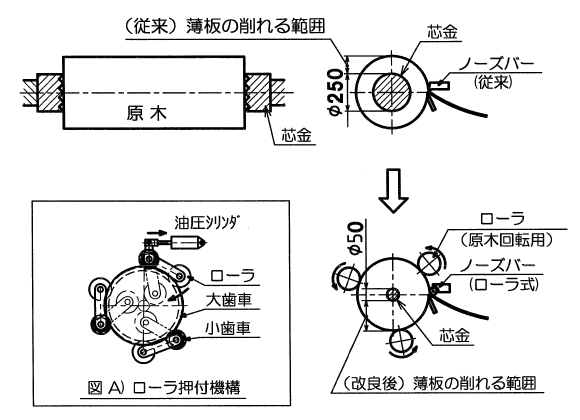
ベニヤレースは、ベニヤ用の板を原木から薄く削り出す機械です。
旋盤では、チャックで鉄の棒をつかんで廻すように、ベニヤレースでは、芯金というもので原木を両側からはさんで支持し、切削用の回転を与えます。
やわらかい木材に回転を与えるため、芯金の直径が最低250mm必要でした。ベニヤ用の板は芯金の手前までしか削りとれません、つまり直径250mm程の材木がすべてムダになってしまうということなのです。
ムダを減らすために芯金を小さくしたい。これが合板業界の古くからの課題でした。
回転と、原木支持の機能を受け持たせるから、芯金が小さくならない。
その役割分担を分けたらどうか?つまり外側からローラを押し付けて回転を与える。
その分芯金を小さくし、原木を支えるだけの大きさにする。
これならうまくいきそうです。
でもここで問題発生・・・ 原木は削られてだんだん小さくなってくるため、押し付けるローラの位置が原木の径に合わせて、変化しなくてはならないのです。
・・・これは、図A)のローラ押付機構を採用することで、クリアしました。
最終的に芯金を50mmまで小さくすることに成功。これまで250mmで捨てていた材木をさらに、50mmの径まで削り込むことが出来るようになりました。
その他こまかい改善もあわせて、特許・実用新案を十数件取得しました。
径の大きな原木が外国から輸入されなくなるという事情もあって、この小径木対応のベニヤレースは一躍脚光をあびたのでした。
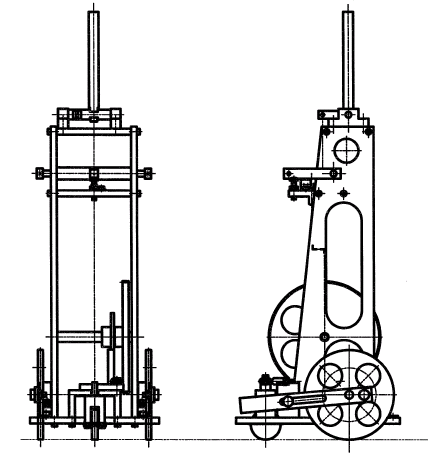
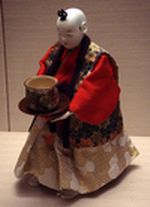
ある会社から「からくり人形」を設計してくれないか?という依頼がありました。
差し出した手の上にお茶を乗せてやると客の前まで運んで行きます。客がお茶を取ると、かるくおじぎをしてストップします。空のお茶椀を置くとUターンしてもとの位置に戻ってくる、あの有名な「茶運び人形」です。
今回の依頼は、まったく昔のままを再現するのではなくモータとセンサを使って動く「現代のからくり人形」です。
社内の教育用に使うということで、「おもしろい、やりましょう」 と2つ返事で引き受けました。
茶運び人形の詳細な図の本がありましたので、それを元にしましたが、クジラのひげで出来たゼンマイをモータに置き換え、木製のパーツをアルミに変更して、旋回、ストップのタイミング機構はセンサを使用しました。
オリジナルをまねて作るということで、そんなに苦労はありませんでしたが、モータもセンサもなかった時代に、よくこれだけのものが作れたな、と先人の知恵の深さに、ただただ感心したものでした。
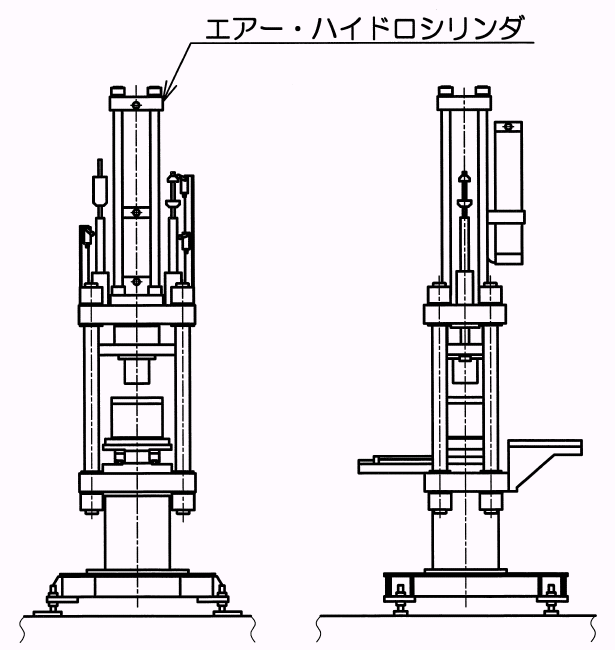
油圧シリンダ・油圧ユニットをエアー・ハイドロシリンダに 置き換えたプレスです。動力源には工場エアーを使用します。
このプレスは、
- 油圧ユニットを無くした
- 機能を絞り込んで コンパクトにした
その結果、従来の油圧プレスの半額以下にコストダウン出来たことと、コスト以外にも次のように、いろいろなメリットが生まれました。
- 油圧ユニット、油圧配管が無くなったことによって・・・
- 消防法申請の必要がなくり、火事の心配もなくなった。
- 油圧ユニット等の面倒なメンテナンスが不要になった。
- 使用している油はごく少量で、劣化がほとんどないため、油交換が不要。
- プレスの占有スペースが半分以下になった。
- 騒音がなくなった、省エネになった。
- 電気制御がシンプルになった。
- 無負荷時のスピードが速くなった。(400mm/sec)
- 製作納期が半分になった。
エアー・ハイドロシリンダは、力のいらないところは、エアーで高速で動かし、力の必要な部分はエアーを油圧に変換して、大きな力を出すという特徴があります。
いろんなプラス要素が集まって、非常に高性能なプレスが完成しました。
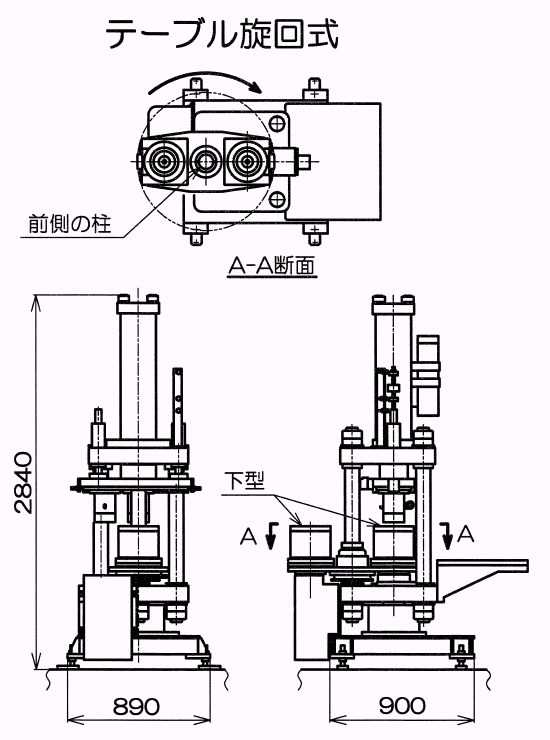
上の30TON エアー・ハイドロプレスの改造型です。
これまでは、下型が1つだったので、ワーク交換の間はプレス作業が出来ないという欠点がありました。
この改造では、下型を回転テーブル上に2コ配置し、下型交換機能を持たせました。
その結果、プレス作業中にワークを交換することが出来、大幅に作業時間を短縮することが出来ました。
一番の特徴は、従来の4本柱から、3本柱に変更したことです。
従来の4本柱のままで回転テーブルを載せると、回転スペース確保のためプレスを大幅に広げる必要があります。
しかし、3本柱にして前側の柱を1本にし、しかもその柱を回転の中心軸として使用することで、従来の大きさのまま、テーブルを回転させることができます。
まさにコロンブスの卵的な発想によって、剛性も十分で、非常にシンプルかつ、スマートなプレスにし上がりました。